Trace DC250
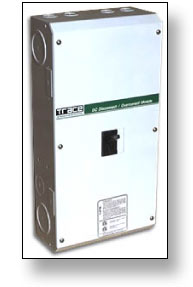
The original concept for the DC250 was to use a fused
pull out similar to Ananda until John Wiles steered
me to the Heinemann GJ1 Series breaker. A breaker
made a lot more sense because those pull outs were
often difficult to actually pull out. The UL specs
have guidelines to follow for minimum bending room
and I cut it down to the bare minimum. Allowing for
more wiring room would have made the boxes larger
and more expensive. It was a couple of years later
that I actually wired up a dual SW power panel with
4/0 cable. That experience was a real eye opener for
me. The DC250 was a bare bones box built for DC only.
There was one DC load breaker for a DC refrigerator
or power shed light. Later on requests came in for
more breaker slots, so I added three more DC breaker
positions. I still did not fully understand the significance
of disconnects for PV controllers, but the additional
breaker slots seemed to satisfy this requirement.
It seemed odd to have breakers protruding out the
sides, but that was the only option available at the
time. In ten years there have been no problems with
this arrangement that I am aware of. The DC250 also
has an optional tin plated machined block of aluminum
for connection of negative conductors. It also had
a 500 amp shunt as an option. Since Trace was an inverter
company, we made the inverter breaker standard and
the charge controller with its breakers optional.
This was just the opposite of Heliotrope. The Trace
box originally sold for $295. It may have been basic,
but it was priced right. I still believe the success
of the DC250 had a lot to do with the demise of Ananda
and Heliotrope. It is interesting to note that the
same DC250 is still sold today by Xantrex.
Trace Power Panel
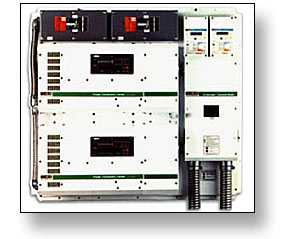
I had seen only a couple of real installations by
the mid 1990’s. Remember, I’m located just North of
Seattle. The sun doesn’t seem to work up here very
often. There was one particularly nice installation
on a mountain top in Ukiah CA that Doug Pratt was
kind enough to show me. I was amazed at how well all
the different boxes had been connected together using
conduit and gutters. It was also obvious to me at
this site that every single installation in the industry
was a custom one-off design. A year or so later after
having created the Trace C-40 solar charge controller,
there were finally enough Trace components to build
a standardized system.
Enter the 400 pound gorilla, the Trace Power Panel.
There was a fair amount of risk in developing the
Power Panel. The industry certainly needed something
that was standard, but we worried that professional
installers would feel like they were being cut out
of some value added income. In reality, they made
profit on the Trace wiring simply from price mark
up. Recently I reassembled my old Trace dual power
panel for the picture at the front of this article.
NEVER AGAIN! It didn’t get any lighter and I didn’t
get any younger.
The only non Trace product on the Power Panel was
the AC bypass switch made by Square D. In 1997, I
began building a house in Arlington near the Trace
factory. I thought that it might be wise to use an
inverter to provide all the power during the construction
phase just to see how our customers lived. During
the construction phase I learned a few things about
the Power Panel that needed some attention.
- There was no way to hook up the Trace 240 volt autoformer in a clean tidy manner.
- The back plate should have been made up of two pieces so it could be sold as a separate piece and shippable via UPS. This also meant that the back plate needed to be made from a lighter gauge steel. The 12 gauge steel back plate was very heavy all by itself.