A little History
The first commercially available circuit breaker boxes made for the RE industry came in around 1989 from Photron. These boxes use paralelled breakers for added current capacity on the inverter curcuit. The boxes were not UL listed but were much better than nothing. Lawrence boxes used paralleled breakers for added current capacity on the inverter circuit. The boxes were not UL listed but were much better than nothing. Lawrence Jennings was a real pioneer in those early days. Our industry was called Alternative Energy back then.
The first commercially available circuit breaker boxes made for the RE industry came in around 1989 from Photron. These boxes use paralelled breakers for added current capacity on the inverter curcuit. The boxes were not UL listed but were much better than nothing. Lawrence boxes used paralleled breakers for added current capacity on the inverter circuit. The boxes were not UL listed but were much better than nothing. Lawrence Jennings was a real pioneer in those early days. Our industry was called Alternative Energy back then.
A little later, Ananda Power came on the scene with
a fully listed AC / DC box. The breaker boxes were
usually custom built for each installation though.
They had standard versions, but since each installation
was different, they advocated custom fitting features
to the installation. They had standard versions, but
since each installation was different, they advocated
custom fitting the features to the installation. This
made it almost impossible for distributors to stock
the right product. The Ananda engineers built flexibility
into each power center; such systems were quite complicated.
They did not allow customizing in the field to any
degree, so things had to be planned in advance by
the installer and distributor. The retail price of
this custom solution ran $1000 or more. The Ananda
Power System quickly became the industry standard
due to its UL listing and lack of competition. Now
customers could actually get their renewable energy
system inspected to NEC compliance.
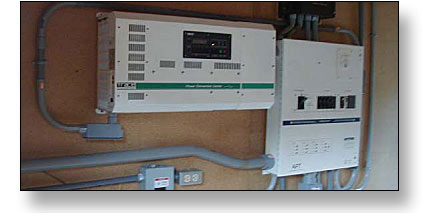
Ananda Power Center with a Trace SW and conduit box.
During the early 1990’s when Ananda was gaining in
popularity, I was very busy at Trace Engineering doing
the mechanical engineering on the SW and DR inverters.
The industry standard inverter at the time was the
Trace U series. I never made the U series able to
accept battery cable conduit because I had little
knowledge of the NEC. As it turns out, the industry
was just learning about the NEC. Remember, the inverter
industry was fueled by marijuana growers in Northern
California and they didn’t have much use for inspectors.
The Trace DR and SW series inverters were the first
in the industry to have this NEC compliance addressed
by virtue of conduit boxes among other mechanical
design aspects. Ananda boxes concentrated heavily
on DC load circuits. I figured that if you had a modern,
efficient and reliable inverter, why would you need
so many DC circuits? That notion was somewhat naïve
on my part since I had actually never yet seen a real
off-grid installation. Another aspect of the Ananda
box was its high cost. It used a nice class T pull-out
fuse for inverter current protection and breakers
for all other circuits. The high cost, I figured,
was due to the custom nature of this product as well
as low quantities that have always plagued our industry.
It seemed that there should be a code compliant solution
to address the inverter battery over-current protection
and disconnect that was affordable. None existed,
so I began designing the Trace DC250, (1994 or 95).