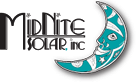


How lightning protection works.
By Robin Gudgel
MidNite Solar Inc.
Lightning comes into wiring common mode. What common mode means is that the PV positive and PV negative as well as AC positive and AC negative rise at the same level from the near lightning strike. Let's just talk about PV input circuits at the moment knowing the battery and AC react the same. You have long wires coming from the PV array to the controller, sometimes very long. These wires act as an antenna. When a surge comes in the vicinity of the wires, it induces voltage. The closer the strike, the higher the voltage induced into the wires. Since the surge is raising the voltage equally in the plus and minus wires, there is no danger to the low voltage transistors in the unit until the surge finally finds a path to earth ground. So what happens is the voltage builds up on the PV + and PV- input or battery plus and battery minus. It keeps on building higher and higher. This all happens very quickly of course.
Now all UL and ETL listed products are required to pass a hi-pot test at the factory. This test is typically 1000VAC plus twice the peak working voltage. We convert this to the equivalent DC voltage which is 1.414 times higher than the AC requirement. There are sometimes advantages in using this higher DC voltage due to parasitic capacitance that can make the product fail when using AC.
In the case of our charge controller, we are required to connect all four of the terminal block wires together, PV+, PV-, Bat+ and Bat-. All four of these connections are connected at the same time to one lead of the hi-pot machine. The other lead of the machine is attached to the casting. The casting represents ground since all equipment enclosures are supposed to be connected to earth ground. Once these two connections are made, we push the GO button on the hi-pot machine. It slowly ramps up from zero volts to 2300 volts DC. It holds the voltage at 2300 volts for one second. The intent here is to check the insulation between all of the electrical circuits inside the controller to ground (the casting). If the unit withstands this 2300VDC for one second without drawing more than 3 milliamps of current, the test automatically terminates. If the product under test does not make it, the machine stops, records the voltage where breakdown occurred and turns on loud buzzers and bright lights. You then have to go find out what was built wrong, fix it, and run the test again. A failed hi-pot test does not happen very often and depending on what went wrong, it can damage the product.
There will be one point where the insulation broke down or there was insufficient distance from a circuit board trace to a casting stand off or something like this. When a product leaves the factory and has a UL or ETL label applied, you can be assured the product has passed this test. The test is required to insure we are building a safe product. You do not want any of the live circuits breaking down to the enclosure case (the casting). This would be dangerous for anyone touching the case which is supposed to be at ground potential.
How does lightning come into play with this hi-pot test? We know that the product was tested to be good to 2300VDC in the case of our controller. Remember, we tied the plus and minus wires together and applied a very high voltage to the circuit. Because we had them all tied together, it did not cause a problem with the low voltage parts in the product. Even though there was a high voltage applied, the difference between leads of the individual components is zero. That is until there is a breakdown in the insulation or air gaps designed to withstand this high voltage. When there is a breakdown, the hi-pot machine will only put out 3 milliamps. This usually does not hurt the product. The breakdown point gets corrected, the product gets tested again and hi-potted again.
Now when a real near lightning strike is induced into the wiring of a system, a very similar thing happens as the hi-pot test. The lightning will continue to rise sometimes to 100,000 volts. There are no consumer products made that can withstand that high of induced voltage. They typically have about 10 to 20% margin of safety over and above the 2300V requirement. IT costs money and space to have a higher breakdown voltage, so design margins are typically slim.
OK, now that the lightning has been induced into the wiring and it reached 3000 volts, we can estimate that someplace inside the controller is going to breakdown and arc over to the case which is connected to earth ground. The lightning is not limited to only 3 milliamps of current. It can go well over 3000 amps.
Another thing happens as the circuits break down. The lightning will continue rising and the circuits may breakdown at 100 different places at the same time. Now you can imagine the mess that comes from thousands of amps flowing in 100 different places inside that metal casting. The product will be toast. There is no way to rebuild a unit that has been subjected to this type of damage.
Now let's add an SPD300 to the input of the controller. When lightning gets induced into the PV wires, it starts rising, but when the voltage reaches 385 volts, the SPD begins conducting. The SPD has thermal metal oxide varistors connected from PV+ to ground and from PV- to ground. Depending on how close the strike is, there could be 100,000 amps behind the surge. The MidNite surge arrestors are good for up to 115,000 amps. The higher the current, the higher the voltage will rise even though the SPD is trying to clamp the voltage down. We have measured about 900 volts of clamp with a 3000 amp surge. UL uses 3000 amps as their simulated lightning surge. Since each controller was tested at the factory to be able to withstand at least 2300 volts, a 900 volt /3000 amp surge will not hurt the unit. If the lightning strike was a direct hit, there may be no saving the product or SPD. IT all depends on where the lightning entered the wiring.
Resistance of the wiring is your friend in this case. The resistance offers impedance to the surge and gives the SPD a chance to act. We were able to test our SPD's with a 40,000 amp surge at 22,000 volts. I did not think you could get 40,000 amps through 12AWG wire, but I was terribly wrong. The lightning surge is so fast that the wire just passes the high current right on through.
We have some videos on our website that show how our SPD's work. They are worth checking out. Does this help?
MidNite Solar Inc.
Lightning comes into wiring common mode. What common mode means is that the PV positive and PV negative as well as AC positive and AC negative rise at the same level from the near lightning strike. Let's just talk about PV input circuits at the moment knowing the battery and AC react the same. You have long wires coming from the PV array to the controller, sometimes very long. These wires act as an antenna. When a surge comes in the vicinity of the wires, it induces voltage. The closer the strike, the higher the voltage induced into the wires. Since the surge is raising the voltage equally in the plus and minus wires, there is no danger to the low voltage transistors in the unit until the surge finally finds a path to earth ground. So what happens is the voltage builds up on the PV + and PV- input or battery plus and battery minus. It keeps on building higher and higher. This all happens very quickly of course.
Now all UL and ETL listed products are required to pass a hi-pot test at the factory. This test is typically 1000VAC plus twice the peak working voltage. We convert this to the equivalent DC voltage which is 1.414 times higher than the AC requirement. There are sometimes advantages in using this higher DC voltage due to parasitic capacitance that can make the product fail when using AC.
In the case of our charge controller, we are required to connect all four of the terminal block wires together, PV+, PV-, Bat+ and Bat-. All four of these connections are connected at the same time to one lead of the hi-pot machine. The other lead of the machine is attached to the casting. The casting represents ground since all equipment enclosures are supposed to be connected to earth ground. Once these two connections are made, we push the GO button on the hi-pot machine. It slowly ramps up from zero volts to 2300 volts DC. It holds the voltage at 2300 volts for one second. The intent here is to check the insulation between all of the electrical circuits inside the controller to ground (the casting). If the unit withstands this 2300VDC for one second without drawing more than 3 milliamps of current, the test automatically terminates. If the product under test does not make it, the machine stops, records the voltage where breakdown occurred and turns on loud buzzers and bright lights. You then have to go find out what was built wrong, fix it, and run the test again. A failed hi-pot test does not happen very often and depending on what went wrong, it can damage the product.
There will be one point where the insulation broke down or there was insufficient distance from a circuit board trace to a casting stand off or something like this. When a product leaves the factory and has a UL or ETL label applied, you can be assured the product has passed this test. The test is required to insure we are building a safe product. You do not want any of the live circuits breaking down to the enclosure case (the casting). This would be dangerous for anyone touching the case which is supposed to be at ground potential.
How does lightning come into play with this hi-pot test? We know that the product was tested to be good to 2300VDC in the case of our controller. Remember, we tied the plus and minus wires together and applied a very high voltage to the circuit. Because we had them all tied together, it did not cause a problem with the low voltage parts in the product. Even though there was a high voltage applied, the difference between leads of the individual components is zero. That is until there is a breakdown in the insulation or air gaps designed to withstand this high voltage. When there is a breakdown, the hi-pot machine will only put out 3 milliamps. This usually does not hurt the product. The breakdown point gets corrected, the product gets tested again and hi-potted again.
Now when a real near lightning strike is induced into the wiring of a system, a very similar thing happens as the hi-pot test. The lightning will continue to rise sometimes to 100,000 volts. There are no consumer products made that can withstand that high of induced voltage. They typically have about 10 to 20% margin of safety over and above the 2300V requirement. IT costs money and space to have a higher breakdown voltage, so design margins are typically slim.
OK, now that the lightning has been induced into the wiring and it reached 3000 volts, we can estimate that someplace inside the controller is going to breakdown and arc over to the case which is connected to earth ground. The lightning is not limited to only 3 milliamps of current. It can go well over 3000 amps.
Another thing happens as the circuits break down. The lightning will continue rising and the circuits may breakdown at 100 different places at the same time. Now you can imagine the mess that comes from thousands of amps flowing in 100 different places inside that metal casting. The product will be toast. There is no way to rebuild a unit that has been subjected to this type of damage.
Now let's add an SPD300 to the input of the controller. When lightning gets induced into the PV wires, it starts rising, but when the voltage reaches 385 volts, the SPD begins conducting. The SPD has thermal metal oxide varistors connected from PV+ to ground and from PV- to ground. Depending on how close the strike is, there could be 100,000 amps behind the surge. The MidNite surge arrestors are good for up to 115,000 amps. The higher the current, the higher the voltage will rise even though the SPD is trying to clamp the voltage down. We have measured about 900 volts of clamp with a 3000 amp surge. UL uses 3000 amps as their simulated lightning surge. Since each controller was tested at the factory to be able to withstand at least 2300 volts, a 900 volt /3000 amp surge will not hurt the unit. If the lightning strike was a direct hit, there may be no saving the product or SPD. IT all depends on where the lightning entered the wiring.
Resistance of the wiring is your friend in this case. The resistance offers impedance to the surge and gives the SPD a chance to act. We were able to test our SPD's with a 40,000 amp surge at 22,000 volts. I did not think you could get 40,000 amps through 12AWG wire, but I was terribly wrong. The lightning surge is so fast that the wire just passes the high current right on through.
We have some videos on our website that show how our SPD's work. They are worth checking out. Does this help?